|
|
Workshop
|
|
How my guitars are produced. |
|
Before I can make an instrument I have to chose its
materials. Because I attach high importance on the quality
of the materials I use, I buy all the wood personally from
its producers. In order to do so I do not shy away from
travelling all over Europe to get only the best wood for
my guitars – e.g. I go to Switzerland or Italy. Important
aspects of the quality are density, stiffness and look.
Special care is neccessary when chosing the woods for the
guitar tops. I am convinced that the top of a plucked
instrument is its core piece and has a huge influence on
the sound. That's why I have always focused on
perfectioning my tops.
My prefered woods here are spruce and cedar, but I also
use redwood. All the other parts are made from many
different traditional tonewoods like maple, rosewood,
mahogany, alder, ebony, cherry, spanisch cedar or bubinga.
All these woods mature individually in my workshop. |
|
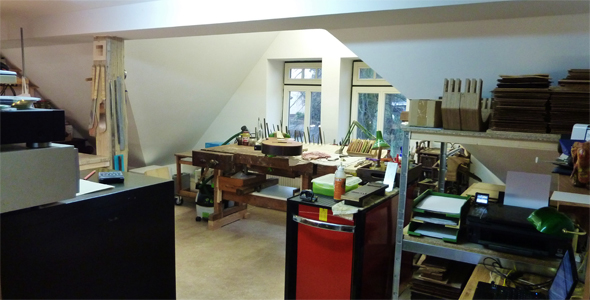
|
|
When I begin making a guitar I pick the woods from my
stock by sound characteristics and look. But because both
criteria surely are not independent from subjective
judgements you are very welcome to come to my workshop, so
we can chose the right woods for your ideal instrument
together. In the end it shall comply with your wishes,
doesn't it? |
|
Each step in the creation
of my instruments consists of diligent hand work. Only if
each and every single part of the instrument has been made
by me personally, I'll be able to ensure constant a
quality of my products. I use machines for very rough
tasks only. Also the ribs get bended by hand. Once they
are in position I can glue the pieces together wich
already gives the instrument its typical shape. Afterwards
the surfaces get polished and varnished. As varnish I use
different synthetic resins, oils or shellack. Using
shellack needs a lot of time and care, but in the end it
gives a very thin varnish which benefits the sound of the
finished instrument.
|
|
As part of the adjustment of my instruments I take
special care of the intonation. This means I adjust the
definition of the frets' pitches through compensation at
nut and saddle. |
|
During my adjucation at
university I gained knowledge in producing and working
with thermally modified wood. I can artificially mature
and refine wood with heat in a special method I developed
myself. This modification leads to a more dry wood than
maturing in a dry place alone could ever do. Because of
this it is more resistent against variations in air
temperature and humidity. Further more it has a positive
influence on the vibration of the wood and thus the
resonance of the instrument.
As a side effect the wood also gets darker the more heat
is used on it which makes a larger scale of visual effects
possible. I even have the impression that thermally
modified spruce narrows its sound to cedar, so you can
kind of create a hybrid between those two woods.
However, this laborious technique cannot be used to turn
wood of bad quality into a high quality one, it can only
make the best out of the wood you already have. I use
thermally modified wood for guitar tops only anyway, which
– as I have already mentioned – have the most influence on
the sound.
The vacuum-stove I have designed specially for this matter
is able to make almost unscented thermally modified wood,
which is remarkable, because it usually tends to smell far
too bad to be used for instruments! |
|
Do you have got any further
questions? Do not hesitate to contact me! If you do not
get me on phone right away, I'll answer your messages as
soon as possible.
|
|